What is Porosity in Welding: Essential Tips for Getting Flawless Welds
What is Porosity in Welding: Essential Tips for Getting Flawless Welds
Blog Article
Porosity in Welding: Identifying Common Issues and Implementing Finest Practices for Avoidance
Porosity in welding is a prevalent concern that usually goes undetected up until it causes significant problems with the integrity of welds. This common defect can compromise the strength and resilience of welded frameworks, posing security threats and resulting in costly rework. By understanding the origin triggers of porosity and applying effective prevention methods, welders can substantially boost the quality and reliability of their welds. In this discussion, we will certainly check out the essential elements adding to porosity development, analyze its destructive results on weld performance, and review the most effective practices that can be adopted to lessen porosity incident in welding processes.
Typical Causes of Porosity
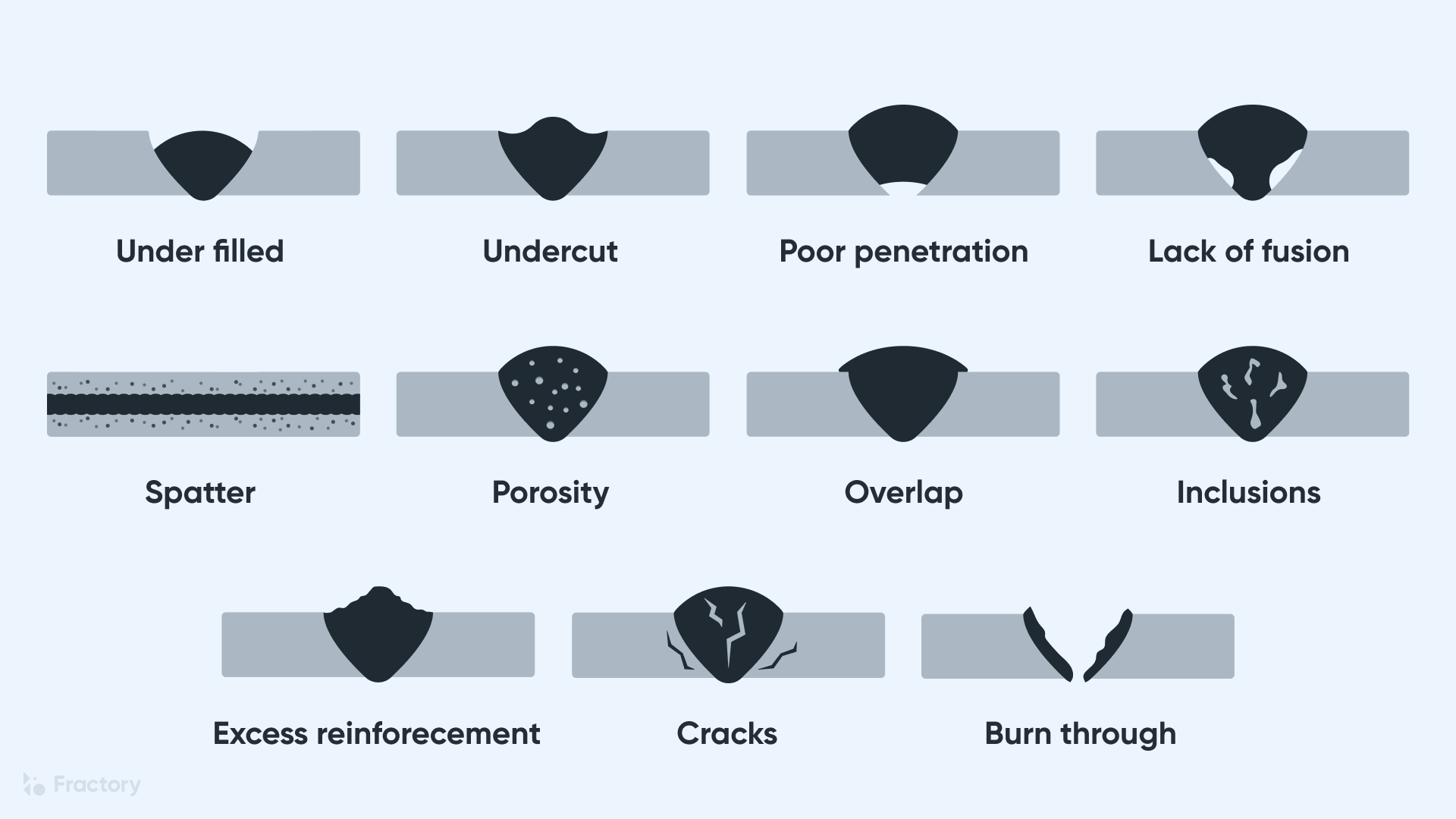
Making use of unclean or damp filler products can introduce contaminations into the weld, contributing to porosity problems. To minimize these usual causes of porosity, comprehensive cleansing of base metals, correct protecting gas selection, and adherence to optimum welding criteria are necessary methods in accomplishing top quality, porosity-free welds.
Effect of Porosity on Weld Quality

The presence of porosity in welding can significantly compromise the structural honesty and mechanical buildings of bonded joints. Porosity creates spaces within the weld steel, damaging its general stamina and load-bearing capacity. These gaps function as anxiety concentration factors, making the weld a lot more prone to fracturing and failure under used loads. Furthermore, porosity can lower the weld's resistance to rust and other ecological aspects, further lessening its durability and efficiency.
Welds with high porosity degrees have a tendency to show reduced impact toughness and decreased capacity to warp plastically prior to fracturing. Porosity can hinder the weld's capacity to effectively transmit forces, leading to early weld failure and possible safety and security risks in important frameworks.
Ideal Practices for Porosity Avoidance
To enhance the architectural integrity and quality of welded joints, what specific steps can be carried out to lessen the incident of porosity throughout the welding process? Utilizing the correct welding technique for the particular material being welded, such as adjusting the welding angle and gun setting, can additionally stop porosity. Normal examination of welds and immediate removal of any type of problems recognized throughout the welding procedure are crucial techniques to avoid porosity and produce high-quality welds.
Importance of Correct Welding Techniques
Carrying out appropriate welding methods is critical in making certain the structural stability and high quality of welded joints, developing upon the foundation of efficient porosity avoidance steps. Extreme heat can lead to increased porosity due to the entrapment of gases in the weld pool. In i loved this addition, making use of the proper welding specifications, such as voltage, present, and travel speed, is critical for accomplishing audio welds with marginal porosity.
Moreover, the option of welding process, whether it be MIG, TIG, or stick welding, should straighten with the certain requirements of the job to guarantee optimal outcomes. Appropriate cleansing and preparation of the base metal, in addition to selecting the best filler product, are additionally essential components of competent welding methods. By sticking to these ideal methods, welders can decrease the risk of porosity formation and generate top notch, structurally audio welds.

Examining and Quality Assurance Procedures
Quality assurance measures play a vital role in verifying the stability and dependability of bonded joints. Evaluating treatments are important to spot more tips here and protect against porosity in welding, making sure the strength and toughness of the end product. Non-destructive testing approaches such as ultrasonic screening, radiographic testing, and aesthetic examination are generally utilized to identify possible flaws like porosity. These techniques permit the assessment of weld high quality without compromising the stability of the joint. What is Porosity.
Performing pre-weld and post-weld evaluations is additionally crucial in preserving top quality control criteria. Pre-weld examinations involve verifying the materials, equipment settings, and sanitation of the workspace to avoid contamination. Post-weld evaluations, on the other hand, assess the final weld for any type of issues, including porosity, and validate that it fulfills defined criteria. Applying a thorough top quality control plan that consists of comprehensive screening procedures and examinations is extremely important to decreasing porosity check my reference issues and ensuring the general top quality of welded joints.
Verdict
To conclude, porosity in welding can be a typical issue that affects the top quality of welds. By identifying the common root causes of porosity and executing finest methods for avoidance, such as appropriate welding methods and screening steps, welders can make certain excellent quality and trusted welds. It is vital to prioritize avoidance methods to decrease the event of porosity and maintain the honesty of bonded frameworks.
Report this page